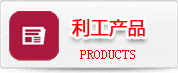
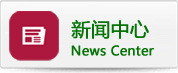
离心泵常见故障及排除
离心泵应用广泛,有多种样式和配置可供选择。本文重点介绍了National Oilwell公司单级悬臂式离心泵。自最初设计以来,已经售出了数千台此类泵,并已证明只要应用正确、维护得当,其可靠性极高。与任何设备一样,设计、制造方法、公差、材料质量、加工程序和装配方法都是确保设备可靠性和功能性的关键。许多公司都曾试图复制National Oilwell公司设计的离心泵产品线,然而,只有National Oilwell公司的工程部门才知道提供高质量泵所需的精确尺寸、公差、负载能力和设计参数,以确保最长的运行时间和最高的性能。
离心泵由旋转部分和静止部分组成,旋转部分由轴、轴承、机械密封(如有)和叶轮组成。静止部分包括机架、填料函和壳体。图 1 将有助于识别离心泵的主要零部件。
叶轮是泵的关键零件,对液体产生离心力,从而使液体加速。一旦壳体内充满液体并启动泵驱动机,泵的旋转组件就会开始旋转。当叶轮旋转时,叶轮吸入孔处会形成一个低压区,供液罐中液体表面的大气压力会释放该低压区。大气压力大于低压区,将液体推入泵中。离心力将液体从叶轮吸入孔推向叶轮的外径。这将液体加速到由叶轮直径和转速决定的速度。泵壳体利用液体速度并将速度转换为压头。轴只是用于将所需动力和转速传递给叶轮的装置。如果泵壳体、叶轮或轴发生故障,泵将无法按设计工作。
离心泵是一种相对简单的机械设备,但其使用方式可能会导致故障、效率降低或严重损坏。泵的问题一般分为以下几类:
1) 吸入条件不足/空气渗入
2) 流量不足
3) 机械/磨损
4) 其它(如润滑等)
吸入条件不足会导致离心泵严重损坏,在某些情况下会导致泵流量为零。这可能是由于空气滞留在壳体中时发生的蒸汽堵塞(汽锁)造成的。请记住,当泵启动且叶轮旋转时,叶轮的吸入孔附近会形成一个低压区。如果壳体或液体中存在空气,则空气会移动到低压区,阻止液体进入叶轮。为了使非自吸式离心泵正常运行,必须保证泵内没有空气。空气可通过多种方式进入泵内。如果泵没有正确灌注,请检查是否存在以下情况:
1) 在启动泵之前,将液体完全灌满泵壳体和吸入管路,并清除所有空气。
2) 壳体出口法兰的方向是否高于吸入法兰?空气是向上而不是向下流动的。如果出口法兰位于吸入法兰下方,则空气会滞留在壳体顶部。当泵启动时,空气将移动到低压区,阻止液体进入或减少进入泵的液体量。
3) 确保吸入管路从供液罐向上通向泵的吸入口。空气可能会被困在上行和下行的吸入管中。当泵启动时,气泡会从该滞留区进入低压区。在启动泵之前,应消除该滞留区或安装排气阀以排出所有空气。
4) 供液罐表面是否形成空气涡流?如果吸入管路没有充分浸没,就会形成空气漩涡,空气就会进入泵的吸入口。为了消除空气漩涡,可增加供液罐中的液体深度、使用更大的吸入管、降低输送的流量 或安装挡板。
图2显示了防止出现涡流所需的吸入管上方的浸没深度。所需的浸没深度取决于液体进入吸入管时的速度。液体速度受体积和管道直径的影响,可参考速度栏下的管道摩擦损失表来确定。例如,通过 SCH 40、8 英寸管道的1000 GPM流量,其流速为6.4 英尺/秒。流速为6.4 英尺/秒的吸入管需要在吸入管入口上方具有约3英尺的液面。在此示例中,如果供液罐的液面低于吸入管入口上方3英尺,就会形成空气漩涡,导致泵汽锁。为了防止出现漩涡,必须将供液罐液面保持在3英尺以上、降低管路速度或安装挡板,如图3所示
对于向下弯向供液罐底部的吸入管线,可以在吸入管线周围水平方向安装一块挡板,以获得相同的结果。
通过安装挡板,可降低挡板边缘的液体速度。这样就能在形成空气漩涡之前将供液罐抽至较低的液位。如果输送流量为1000 GPM,并安装了一块18” 的挡板,则挡板边缘处的流速为1.26 ft/s。这样就可以在形成漩涡之前将供液罐液位抽到距离挡板1 ft以内。
5) 确保所有吸入法兰都已拧紧。即使法兰没有泄漏液体,松动的法兰也会使空气进入系统。
6) 确保有足够的净正吸入压头(NPSHa)。泵曲线包含泵正常运行所需的最小值。NPSHa值不足会导致汽蚀,甚至可能导致泵完全失效。NPSHa值会受到摩擦损失、供液罐相对于泵中心线的高度、液体温度、工作地点海拔高度和液体比重的影响。有关汽蚀和计算 NPSHa值的详细信息,请参阅美国National Oilwell公司 2004 年出版的文章《Sizing Centrifugal Pumps》。
7) 泵的吸入管路(通径)应始终等于或大于泵的吸入法兰(通径)。选择适当尺寸的吸入管路,使液体流速保持在5-8.5 ft/s之间。
8) 确保吸入阀门完全打开,切勿通过调节吸入阀门来节流泵的流量。
9) 确保吸入管路膨胀节内管没有塌陷。当内管已塌陷并限制了泵的流量时,外管可能看起来正常。对于油基液体,应使用丁腈橡胶管膨胀节,而不是氯丁橡胶管。
10) 确保泵叶轮中没有异物。法兰盖、蓝色牛仔裤、抹布、扳手和其它物体通常会卡在泵内。
11) 确认泵的旋转方向正确。在吸入法兰附近的外壳上可以找到旋转方向的箭头标志。
12) 确保液体中没有夹带空气或气体。夹带的空气会迁移到叶轮吸入孔处的低压区,并与其它气泡一起形成大气泡,阻碍液体的流动。确保回流管路低于液体表面并远离泵的吸入口,如图 4 所示。
如果泵正在输送液体,但流量小于预期,原因可能是上述吸入条件不足、压头不足、压头过高、管路堵塞、汽蚀、泵磨损或设备磨损。吸入条件不足可能导致出口流量为零,但也可能不太严重,导致流量降低。如果存在流量不足的情况,请务必检查之前在“吸入条件不足”部分所述的条件。如果泵的规格尺寸、叶轮直径或驱动转速不合适,则可能无法产生足够的排出压头来克服系统摩擦损失和高程。离心泵是一种压头恒定、容积变化的设备。这与产生恒定容积、变化压力的容积泵相反。离心泵的流量受到背压的限制。当系统背压和泵压头相等时,离心泵产生的流量就会趋于稳定。如果泵产生的压头大于系统所能吸收的压头,则泵的流量将继续增加,直至达到流量曲线的末端。一旦达到流量曲线的末端,汽蚀现象就会开始出现,并可能导致流量的脉动。如果汽蚀现象严重,则会破坏泵的液体端,并可能导致输出量急剧下降。在选择离心泵时,有必要确定系统的摩擦损失和高程,并选择一个叶轮直径和速度,使其与系统摩擦损失、高程和所需流量下的扬程相等。
摩擦曲线可以绘制在泵的曲线上,以确定泵将产生的流量。假设存在一个期望流量为1000 GPM 的系统。系统摩擦和高程损失可在多种流量下确定。在此示例中,高程为20 ft,有长100 ft的新SCH(40)6” 管道,管道末端有1个3” 的喷嘴。这些系统参数会产生高程损失、摩擦损失和喷嘴水头损失。本例中将绘制 0、600、800、1000、1200 和 1400 GPM 的工作点性能。可以参考摩擦损失表和喷嘴损失表来确定损失值。这些可在泵手册和National Oilwell离心泵目录中找到。对于本练习,图 5提供了这些值。可将系统总损失值绘制在泵曲线上,以确定适合该系统的叶轮和转速。在本例中,将使用定速曲线和不同直径的叶轮(也可使用最大叶轮直径的变速曲线)。请参考图6和摩擦损失曲线。离心泵的机械相关问题一般与叶轮、泵壳体、轴承、机械密封或填料有关。叶轮和壳体可能会受到磨损、腐蚀或汽蚀的影响(即使壳体是静止的,也会影响叶轮的性能)。轴承可能会受到对中、润滑、污染、超过功率限制和转速的影响。机械密封会受到安装方法、腐损、发热和润滑的影响。填料会受到安装方法、磨损、润滑和叶轮间隙的影响,从而导致填料函压力过高。
磨损 - 叶轮与泵送的液体接触并高速旋转。因此,这是最容易受到侵蚀的零件。图7显示了叶轮的严重磨损,但请注意,所有叶片的磨损都是平滑且相同的。叶轮磨损会导致压头下降和流量降低。更换磨损的叶轮。注:对于极易磨损的应用,液体端零部件可采用优质材料,如 MagnachromeTM 和 Supreme HardTM。通过以较低的速度运行最大直径的叶轮,也可以延长液体端的使用寿命。叶轮有全开式、半开式和闭式三种。National Oilwell离心泵可提供全开式或半开式叶轮。全开式和半开式叶轮依靠壳体耐磨垫作为叶轮前端。叶轮应位于壳体耐磨垫0.025英寸的范围内。这将产生最大的压头和最有效的运行。随着壳体耐磨垫和叶轮前端开始磨损,这些零部件之间的间隙会增大。这使得一些液体再循环回到低压区(叶轮吸入孔)。当叶轮和壳体间隙磨损到一定程度时,液体再循环会增加。液体再循环的增加会导致排放压头降低和泵效率下降。可以通过调整叶轮与壳体耐磨垫之间的间隙来克服前端磨损,但这会增加叶轮后面的间隙。叶轮后的间隙增大会在填料函区域产生更高的压力,这可能会导致填料过早失效。当性能下降到影响系统运行时,应更换磨损的零部件。
腐蚀 - 腐蚀可能是液体与金属和夹带空气的液体之间的不相容性引起的。液体会削弱或破坏金属,导致泵过早失效。图8显示了一个因腐蚀而失效的填料函。请注意,金属已被破坏得不均匀。应选择与泵送液体兼容的液体端材料。可提供各种耐腐蚀材料的液体端零部件,如 316SS、铝青铜和 MagnachromeTM。在某些情况下,腐蚀会加速零件的损失。
汽蚀 - 造成汽蚀的原因可能是吸入或排出条件不当、泵选择不当、液体温度过高或多种因素共同造成的。汽蚀会严重缩短泵的使用寿命。当液体进入泵时,叶轮吸入孔处的压力会下降。如果可用的吸入压力(NPSHa)不足或系统背压不足,液体就会从液态转变为气态(汽化)。气体形成气泡,当这些气泡从叶轮的内径向外径移动时,压力就会增加。最终,压力增加到足以使气泡破裂的程度。此时,气泡内爆,被气泡曾经占据的空间被液体快速充满。液体在充满该空间时会产生巨大的冲击力,以至于使邻近的金属破裂。图9显示了一个正在坍塌的气泡。气泡中心的水匕首可以每小时 560 英里的速度撞击金属。随着这一过程的不断重复,它将击破液体端零件表面,甚至将填料函、叶轮或壳体击穿一个洞。在检查泵时可以看到汽蚀损坏,严重时还可以听到汽蚀声。严重的汽蚀听起来就像泵在泵送石头。
图10显示了在泵送清洁液体时发生的汽蚀损坏。请注意金属断裂造成的空洞区域的锯齿状边缘。这种损坏可能发生在叶轮、壳体和/或填料函上。
图 11 显示了输送磨蚀性液体的泵发生的汽蚀损伤。断裂发生后,锋利的棱角会被研磨液磨光滑。受损的零件看起来就像用勺子从零件上舀下一块金属。汽蚀会破坏泵的液体端,简单地通过更换零件并不能解决问题。当汽蚀发生时,泵和系统的不能协调工作,泵的液体端将不断受损,直到系统经过合格的工程师或销售人员的审查,并纠正了系统的不良状况或泵的重新配置。
对中及管道 - 泵和驱动机对中不当会导致泵和/或驱动机轴承故障。在工厂组装的设备在装运前均已正确对中。但是,在装运和设备安装过程中的搬运通常会导致对中不准。在安装和配管完成后,对中设备极为重要。管道应独立支撑。泵不应承受吸入或排出管道的重量。建议在泵的吸入和排出侧安装膨胀节。膨胀节可简化管道与泵法兰的对中,并对温度变化引起的管道膨胀和收缩进行补偿。对于油基液体,建议使用带有丁腈橡胶管的膨胀节,以防止内管塌陷。膨胀节塌陷会导致流量受限和泵的汽蚀。联轴器对中的推荐程序是使用千分表,如图12和图13所示。千分表安装在一侧的半联轴器(联轴器轮毂)上,指示器按钮靠在另一侧半联轴器的外径上,以测量偏移偏差。要测量角度偏差,则将千分表定位,使按钮位于另一侧半联轴器外径附近的端面上。除非联轴器制造商另有规定,偏移不对中应限制在0.010英寸T.I.R.(总指示器跳动)以内,角度不对中应限制在0.005英寸 T.I.R. 或联轴器制造商规定的水平。通过拧松驱动机或泵的安装螺栓来调整不对中,并根据需要增加垫片、重新拧紧。如果没有千分表,可以用直尺进行适当的对中。如果所使用的联轴器包含橡胶驱动元件,则这种方法特别有用。要检查偏移不对中,将直尺与两半联轴器的外径对齐。直尺下面不应有间隙。检查相隔90°的两个位置。角度不对中可通过测量两半联轴器端面之间的间隙进行检查。直尺下的间隙不应超过1/64",两半联轴器端面之间的间隙变化不应超过1/64"。参见图14和15。
注:有关联轴器对中的更多参考资料,请参见《Hydraulic Institute》第13版,第117和120 页。
润滑 - 影响润滑的因素包括润滑不足、润滑过度、润滑类型、润滑剂兼容性、温度和受污染的润滑剂。应制定并记录适当的润滑计划。National Oilwell Mission 离心泵轴承(工作转速低于2400 rpm)在组装过程中已充满润滑脂,轴承盖在泵组装过程中加注1/3至1/2的润滑脂。轴承在工厂使用 Chevron SRI-2 润滑脂进行润滑。当重新润滑时,Chevron润滑脂将是最好的选择,因为混合润滑脂有时会导致不相容性问题。Texaco Premium RB,壳牌Dolium-R, Amoco Rycon Premium Grease和Mobilux EP多用途润滑脂也可以接受。这些都是无法通过管道接近的。可用于管道和可接受的润滑脂,按优先顺序为:EXXON Unirex N2, Chevron polyrea EP 2, Texaco Marfac Multipurpose 2, Shell MP (Alvania) 2和Amoco Rycon Premium 2 EP。使用上述轴承润滑脂或同等润滑脂时,在每天工作24小时的情况下,每个轴承每月用标准尺寸的手动润滑脂枪喷5次润滑脂就足够了。运行时间较短时可适当减少。如果不对轴承进行润滑,可能会导致轴承润滑不足和故障。轴承润滑过度会导致轴承箱内充满润滑脂。当轴承箱充满润滑脂时,轴承产生的热量无法消散,可能导致轴承故障。在将润滑脂注入轴承之前,应确保其不含灰尘、水份或其它污染物。使用高压喷雾器清洗泵时,应避免将水注入轴承盖唇形密封下方。如果可能,在清洗之前让泵冷却。用冷水喷洒热泵并导致温度急剧变化会使泵轴承箱内出现真空,从而导致轴承盖唇形密封吸水。在泵轴承箱上安装一个呼吸器,可以防止发生这种情况,应检查呼吸器以确保其未被堵塞。所提供的润滑脂适用于 -5 至260 °F 的温度范围。轴承的工作温度最高可达250 °F。检查润滑情况、泵和驱动机的对中情况以及轴承磨损的迹象。预期运行速度高于2400 rpm的泵应选择油润滑泵。建议使用无洗涤剂的10W30润滑油。泵必须保持水平。应定期检查油位,每运行1-2个月或1000小时更换一次润滑油。不要给泵注油过多,因为油位过高会导致润滑油出现剧烈搅拌、轴承过热。
马力(功率)限制 - 保持在轴承额定马力范围内非常重要。1-1/8” 基座的最大额定功率为 40 HP,1-7/8”基座的最大额定功率为100 HP,2-1/2”基座的最大额定功率为 200 HP。对于皮带驱动的 2-1/2” 泵,额定功率应限制在150 HP。不推荐1-1/8" 和 1-7/8" 泵使用皮带驱动。
机械密封 - 不建议将机械密封用于输送比重大于1.05的液体的1-1/8”和1-7/8”泵。在这些较小的泵上发生的轴偏转会导致密封以不规则的方式磨损,通常会导致密封寿命不足。对于超过此建议要求的机械密封应用,建议使用Magnum或2500 Supreme 2-1/2” 泵。机械密封的密封面需要持续供应液体来润滑。一层薄薄的液膜在密封面的外径处进入密封。当它穿过密封面时,使密封得到润滑,并在达到密封面的ID时蒸发掉。如果这种液体供应中断,密封面可能在几秒钟内被破坏。可以在放大镜下检查失效的密封以确定失效原因。密封面碎裂或开裂可能是由于密封面分离后又撞击在一起造成的,发生汽蚀时可能会出现这种情况。如图16所示,密封面上磨损的凹槽表明密封面分离并被固体颗粒污染,然后闭合。请注意,宽沟槽是正常的磨损模式,但磨损模式中的亮沟槽是由固体污染造成的,这也是发生汽蚀的迹象。汽蚀对密封和泵的寿命有害,必须找出并消除汽蚀的原因。密封面出现大面积裂纹可能表明密封在干燥状态下运行,变热后又被较冷的液体淹没,从而产生热冲击。磨损、热裂或烧焦的气味表明密封处于干运行状态。图17是热裂的示例。只有当泵壳体内充满液体且没有空气和空气夹带的液体时,才能运泵。如果无法始终在充满液体的情况下运行泵,建议使用双机械密封。如果出现干运行的迹象,而且泵操作员坚持认为泵没有在未进水的情况下运行过,则可能是其它因素造成的。在运行油基渣浆时,必须使用苯胺点大于165的柴油。如果苯胺点低于165,则柴油在穿过密封面时就会发生闪蒸。如果燃油在到达密封内径之前发生闪蒸,那么密封面就会变干。在输送温度较高的油基渣浆时也可能出现这种情况。检查柴油的苯胺点,并确保使用的燃油苯胺点大于165。如果无法获得苯胺点高于165的燃油,或者无法避免渣浆温度升高,则建议使用带隔离液储罐的双机械密封。为了延长机械密封的使用寿命,应避免上述问题,并确保密封安装正确。机械密封安装说明可向泵供应商索取。在安装机械密封之前,将叶轮调整至与泵壳体的距离在 0.025英寸以内。在安装密封后将叶轮调向壳体会导致波纹管膨胀。如果波纹管膨胀,当密封面开始磨损时,波纹管将无法进一步膨胀,从而缩短密封的使用寿命。安装密封时应确保波纹管完全压紧。National Oilwell的Olympia双机械密封由隔离液储罐中的液体润滑,而不是由泵送的液体润滑。该密封不会因泵干运行、苯胺点低的油基渣浆或高温渣浆而损坏。
轴填料 - 填料的润滑方式多种多样。填料可以用油脂润滑,也可以用泵送液体润滑,在某些设备中还可以用水冲洗管路润滑。如果润滑系统出现故障,填料会变干、变热、变脆并失效。安装方法不当也会导致失效。填料泵在填料函侧面装有润滑脂加注嘴。每运行24小时,应使用优质水基润滑脂对填料进行润滑。这可以手动进行,也可以安装弹簧加载式油杯。安装填料时应遵守安装说明。安装填料圈时,应使其与前一个填料圈的开口相距180度,最后一个填料圈的开口位置应在向下或6点钟位置。因此,在安装6圈填料时,第一圈填料的开口应向上或在12:00点钟位置,第二圈位于向下位置,第三圈位于向上位置,直到最后一圈位于向下位置。这种配置有助于防止过度泄漏,并确保液体滴入泵滴液盘,而不会沿着轴流向轴承盖。必须让液体以每分钟 8-10 滴的速度从填料中滴出。这有助于润滑填料。安装填料时,填料压盖只能用手指拧紧。让泵运行30分钟,同时确保填料继续有液体滴出。一旦填料达到工作温度,即可缓慢调节填料压盖,直到泵的泄漏量减少到每分钟 8-10 滴。如果不遵守这些程序,将导致填料发热、膨胀和密封脱开。如果填料密封脱开,填料将不再得到液体的充分润滑,并会升温至冒烟和燃烧的程度。如果填料燃烧,则会变脆,无法再正确地密封泵。安装填料时要确保轴或轴套没有深深的沟槽或凹坑。必要时更换这些零件
-江苏海珐机械制造有限公司,化工泵,皮托管泵,旋喷泵,Ni-Hard材质,零汽蚀余量泵,江苏利工,江苏海珐机械,习近平出席中阿合作论坛第十届部长级会议开幕式并发表主旨讲话,中华人民共和国粮食安全保障法,谷神星一号,养老保险,华龙一号,列车运行图,汛期,文旅融合“燃”动夏日,老师别哭,变型金刚,末路狂花钱,老板娘3,极寒之城,蝙蝠侠,庆余年,万相之王,修罗武神,女总裁的上门女婿,九星霸体诀,盖世神医,庆余年第二季,爱情,开袋即食,涂山小红娘,田耕记,家族荣耀之继承着,南城宴,迈腾、迈巴赫,马自达3昂克赛拉,长安欧尚Z6,星瑞,星越L,冶金供应部钢铁研究总院靖江不锈钢泵阀厂,江苏利工集团有限公司,耐磨耐腐蚀Ni-Hard材质。更多资讯,敬请百度查询海珐网站:www.jslgpump.com 和江苏海珐机械中国微博、微信。